NEWS
The Critical Role of Rubber Diaphragms in Filter Press Technology
Date:
2025-06-18
Source:
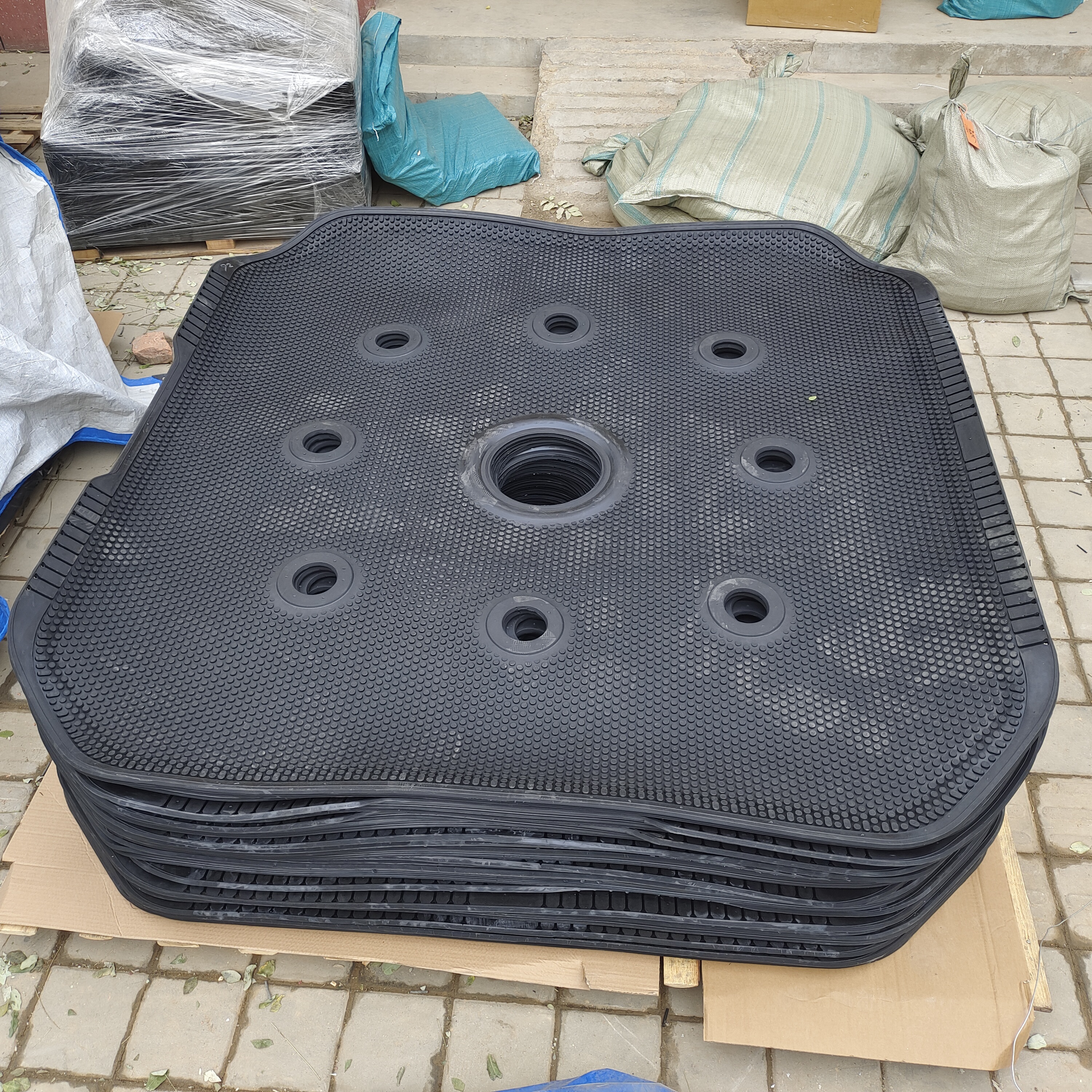
1. Introduction to Filter Press Rubber Diaphragms
Rubber diaphragms are elastomeric components integrated into membrane filter plates, distinguishing them from conventional plate-and-frame or recessed chamber filter presses. These flexible membranes—typically fabricated from NBR (Nitrile Butadiene Rubber), natural rubber, or specialized compounds like fluorocarbon rubber—enable secondary mechanical compression of filter cakes. By applying pressures up to 3.0 MPa after initial slurry feeding, they drastically reduce residual moisture in solid residues, enhancing efficiency in industries ranging from mining to wastewater treatment.
2. Working Principle: How Rubber Diaphragms Transform Filtration
Phase 1: Initial Filtration
Slurry is pumped into chambers formed between paired plates. Solids accumulate on filter cloths, while liquids exit via drainage channels. This primary stage operates at 0.6–1.0 MPa.
Phase 2: Diaphragm Compression
Post-filling, high-pressure fluid (water/compressed air) inflates the rubber diaphragm. This expansion uniformly squeezes the filter cake, collapsing residual pores and expelling trapped liquid. Industrial data show moisture reductions of 15–25% (e.g., titanium dioxide slurries dropping from 28% to 18% humidity).
Phase 3: Air Blow Dewatering (Optional)
Compressed air may penetrate the cake, displacing residual moisture—ideal for cohesive materials like oily sludge.
3. Material Engineering & Design Innovations
Core Materials
- NBR/NR: Cost-effective for general use (pH 5–9, ≤80°C).
- Fluorocarbon Rubber (FKM): Resists aggressive chemicals (acids, solvents) and temperatures up to 120°C.
- Reinforced Composites: Fabric interlayers (e.g., polyester mesh) in rubber-fabric diaphragms enhance tear resistance while maintaining 1.2-mm flexibility.
Structural Advances
- Embedded Sensors: Piezoelectric ceramics monitor diaphragm stress and cake density in real time.
- 3D Flow Grids: Patented surface patterns on plates accelerate filtrate drainage by 25%, preventing clogging.
4. Industrial Applications: Efficiency Metrics
Industry Use Case Performance Gain
Mining Tungsten concentrate Moisture: 14% → 9%; saves $300K/yr transport
Hazardous Waste Oil sludge dewatering Oil content: 15% → <5%, meeting incineration specs
Chemical Processing Lithium battery materials Solid recovery rate: 92% → 97%
5. Technical Advantages Over Conventional Filter Presses
- Energy Savings: Dual-stage compression cuts electricity use by 35% per ton.
- Cycle Time Reduction: Automated squeezing halves processing duration versus manual cake removal.
- Uniform Cake Structure: Diaphragm flexibility eliminates "edge thinning," extending filter cloth life.
6. Emerging Trends & Challenges
Innovations
- Graphene-Enhanced Rubber: 8× higher abrasion resistance and tolerance to pH 1–14 extremes.
- Hybrid Processes: Combining ultrasonic waves or pulsed electric fields with diaphragm pressing to breach sub-8% moisture barriers.
Operational Constraints
- Particle Size Limits: Particles <5 μm may over-compact, reducing permeability.
- Temperature Sensitivity: Standard rubber degrades >120°C; PTFE coatings risk cracking in acids.
7. Conclusion: Toward Smarter, Tougher Diaphragms
Rubber diaphragms epitomize the shift from passive filtration to active solid-liquid separation. As material science advances—such as self-healing elastomers and IoT-enabled pressure control—these components will unlock efficiencies in emerging sectors like biomaterials recovery. Manufacturers like Hebei Linaier Rubber already pioneer specialized formulations, signaling a future where diaphragms are not just consumables, but high-precision tools for sustainable industry.
Key Fact: Modern diaphragm filter presses achieve up to 40% higher throughput per unit area than traditional designs, making them indispensable for high-volume, low-moisture applications.
keywords:
Rubber Diaphragms,Rubber Diaphragms in Filter Press Technology
Related news